APQP (Advanced Product Quality Planning) faser, exempel
APQP (Advanced Product Quality Planning), är på spanska "Advanced Product Quality Planning", är det ett ramverk av förfaranden och tekniker som används för att utveckla produkter inom industrin, särskilt bilindustrin..
Komplexa produkter och leverantörskedjor uppvisar många möjligheter att misslyckas, särskilt när nya produkter lanseras. APQP är en strukturerad process för design av produkter och processer, som syftar till att garantera kundtillfredsställelse med nya produkter eller processer.
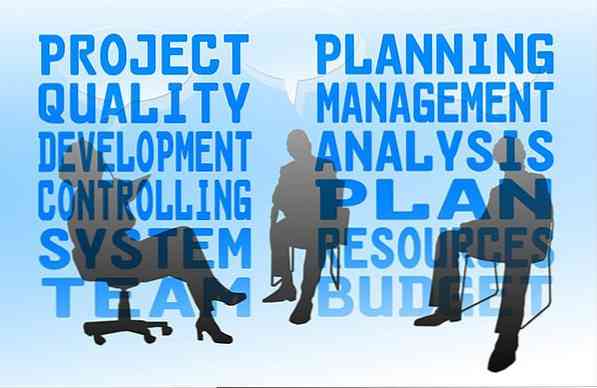
Denna metod använder verktyg och metoder för att minska riskerna för förändringar i en ny produkt eller process.
Dess syfte är att skapa en standardiserad plan för produktkvalitetskrav som gör att leverantörer kan utforma en produkt eller tjänst som uppfyller kunden, underlättar kommunikation och samarbete mellan olika aktiviteter.
I APQP-processen används ett multifunktionslag som omfattar marknadsföring, produktdesign, inköp, produktion och distribution. Denna process används av General Motors, Ford, Chrysler, och dess leverantörer, för sitt produktutvecklingssystem.
index
- 1 fas
- 1.1 Fas 1: Planering och definition av programmet
- 1.2 Fas 2: Design och utveckling av produkten
- 1.3 Fas 3: Design och utveckling av produkttillverkningsprocessen
- 1.4 Fas 4: Process- och produktvalidering
- 1.5 Fas 5: Start, utvärderingar och kontinuerlig förbättring
- 2 Exempel
- 2.1 Var ska man införliva APQP
- 2.2 Branscher som använder den
- 3 referenser
faser
APQP fungerar som en guide i utvecklingsprocessen och också som ett vanligt sätt att dela resultat mellan leverantörer och bilföretag. Den består av fem faser:
Fas 1: Planering och definition av programmet
När kundernas efterfrågan kräver införandet av en ny produkt eller granska en befintlig blir planeringen en central fråga, även innan diskussioner om produktdesign eller redesign.
I denna fas försöker planeringen förstå kundens behov och produktens förväntningar.
Planeringsaktiviteter inkluderar att samla in nödvändiga data för att definiera vad kunden vill ha och sedan använda denna information för att diskutera produktens egenskaper.
Då kan du definiera det kvalitetsprogram som är nödvändigt för att skapa produkten enligt angiven.
Resultatet av detta arbete är produktdesign, tillförlitlighet och kvalitetsmål.
Fas 2: Produktdesign och utveckling
Syftet med denna fas är att slutföra produktdesignen. Det här är också där en utvärdering av produktens lönsamhet kommer till spel. Resultaten från arbetet i denna fas inkluderar:
- Granskning och verifiering av avslutad design.
- Definierade specifikationer för material och utrustningskrav.
- Analys av effekt och felläge för den färdiga konstruktionen för att utvärdera felfel.
- Kontrollplaner fastställda för att skapa produktprototypen.
Fas 3: Design och utveckling av produkttillverkningsprocessen
Denna fas fokuserar på planering av tillverkningsprocessen som kommer att producera den nya eller förbättrade produkten.
Målsättningen är att utforma och utveckla produktionsprocessen med hänsyn till produktens specifikationer och kvalitet samt produktionskostnaderna.
Processen måste kunna producera de kvantiteter som är nödvändiga för att tillfredsställa konsumenternas förväntade efterfrågan samtidigt som effektiviteten bibehålls. Resultaten i denna fas inkluderar:
- En fullständig konfiguration av processflödet.
- En analys av effekt och felläge för hela processen för att identifiera och hantera riskerna.
- Kvalitetsspecifikationer för driftprocessen.
- Förpackning och efterbehandling av produkten.
Fas 4: Process- och produktvalidering
Detta är testfasen för att validera tillverkningsprocessen och slutprodukten. Stegen i denna fas inkluderar:
- Bekräftelse av produktionsprocessens kapacitet och tillförlitlighet. Likaså av kriteriet för godkännande av produktens kvalitet.
- Genomförande av testproduktionskörningar.
- Produkttest för att bekräfta effektiviteten av produktionsmetoden som implementerats.
- Gör nödvändiga justeringar innan du går vidare till nästa fas.
Fas 5: Start, utvärderingar och kontinuerlig förbättring
I denna fas sker lanseringen av storskalig produktion med inriktning på att utvärdera och förbättra processerna.
Bland pelare i denna fas är minskningen av processvariationer, identifiering av problem samt initiering av korrigerande åtgärder för att stödja kontinuerlig förbättring.
Det finns också insamling och utvärdering av feedback från kunder och data relaterade till process effektivitet och kvalitetsplanering. Resultaten inkluderar:
- En bättre produktionsprocess genom att minska processvariationerna.
- Förbättring av kvaliteten vid leverans av produkten och tjänsten till kunden.
- Förbättrad kundnöjdhet.
exempel
Var ska man införliva APQP
- Utveckling av krav från klientens röst, med hjälp av genomförandet av kvalitetsfunktionen.
- Utveckling av en produktkvalitetsplan integrerad i projektschemat.
- Produktdesignaktiviteter som kommunicerar speciella egenskaper eller nycklar till processdesignaktiviteten innan du släpper ut designen. Detta inkluderar nya former och delar, snävare toleranser och nya material.
- Utveckling av testplaner.
- Användning av formell designöversikt för att spåra framsteg.
- Planering, förvärv och installation av lämplig utrustning och verktyg för processen, enligt de designtoleranser som anges av produktdesignkällan.
- Kommunikation av förslag från montage- och tillverkningspersonal på sätt att bättre montera en produkt.
- Upprättande av adekvata kvalitetskontroller för speciella egenskaper eller nycklar till en produkt eller parametrar i en process, som fortfarande riskerar att bli potentiella fel.
- Genomförande av studier av stabilitet och kapacitet för speciella egenskaper för att förstå den nuvarande variationen och därigenom förutsäga framtidens prestanda med statistisk kontroll av processer och processens kapacitet.
Branscher som använder den
Ford Motor Company publicerade den första manuella avancerad kvalitetsplanering för sina leverantörer till början av 80. Detta bidrog Ford leverantörer för att utveckla lämpliga kontroller för att förebygga och upptäcka nya produkter och därmed stödja ansträngningarna av företagens kvalitet.
I slutet av 80-talet använde de största tillverkarna av bilindustrin APQP-programmen. General Motors, Ford och Chrysler hade det implementerat och såg behovet av att förena för att skapa för sina leverantörer en gemensam kärna av produktkvalitetsplaneringsprinciper.
Riktlinjerna fastställdes i början av 1990-talet för att säkerställa att APQP-protokollen följdes i ett standardiserat format.
Företrädare för de tre biltillverkare och American Society for Quality Control skapat en grupp av kvalitetskrav för att få en gemensam förståelse för frågor av gemensamt intresse inom bilindustrin.
Denna metod används nu också av progressiva företag för att garantera kvalitet och prestanda genom planering.
referenser
- Wikipedia, den fria encyklopedin (2018). Avancerad produktkvalitet planering. Hämtad från: en.wikipedia.org.
- NPD Solutions (2018). Avancerad produktkvalitetsplanering. Hämtad från: npd-solutions.com.
- Kvalitet-En (2018). Avancerad produktkvalitetsplanering (APQP). Hämtad från: quality-one.com.
- Baits (2018). De fem faserna i APQP: En översikt över nyckelkraven. Hämtad från: cebos.com.
- David Ingram (2018). Avancerad produktkvalitetsplanering. Småföretag - Chron.com. Hämtad från: smallbusiness.chron.com.